Emerging Trends in Machinery: Tech Shaping Industry 4.0
Industrial Advancements: Trends in Machinery & Equipment Research
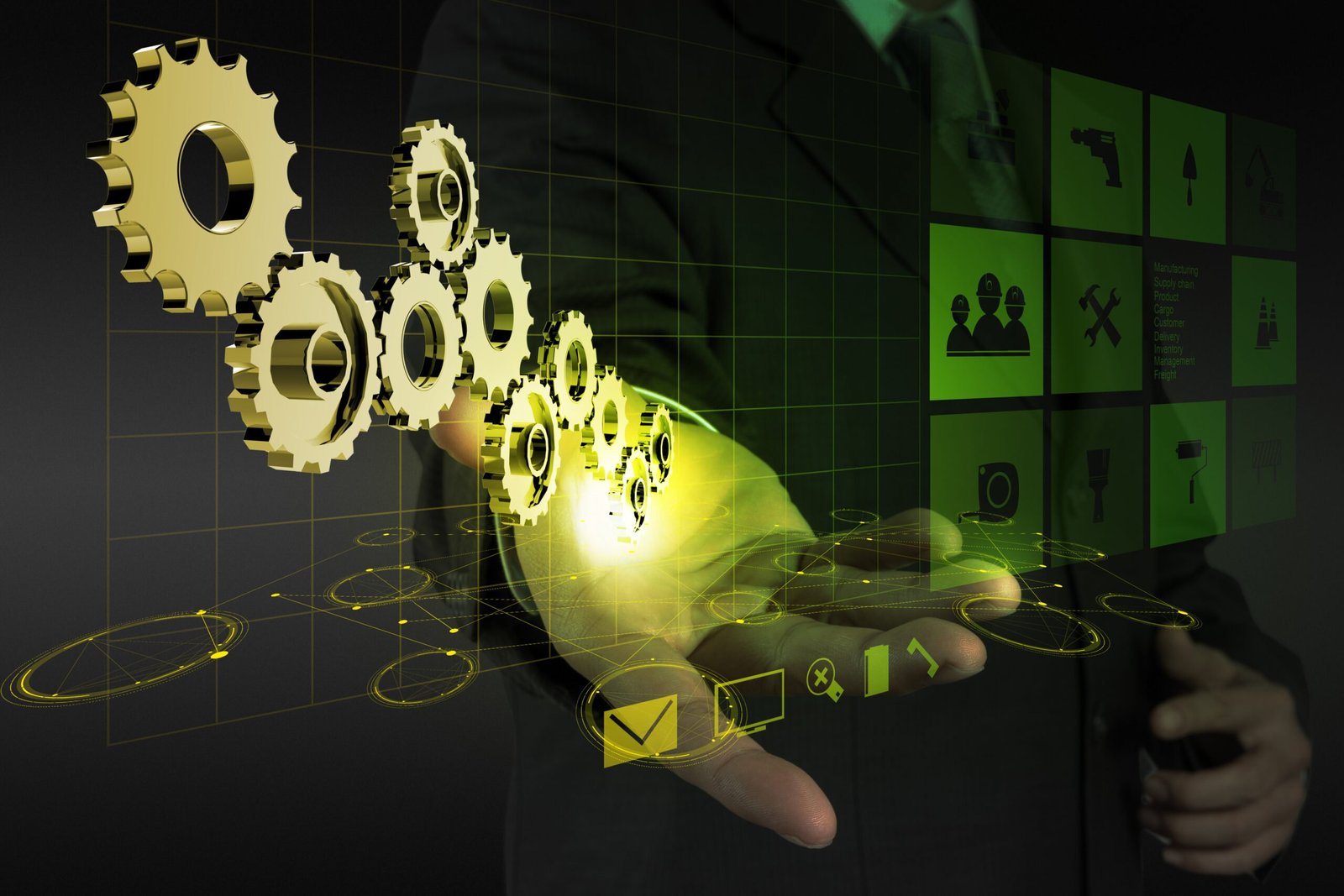
Introduction:
The rapidly evolving landscape of machinery and equipment research is instrumental in bolstering industrial advancements. This dynamic field sees constant innovation, leading to more efficient, sustainable, and cost-effective solutions in manufacturing and production. As industries strive to keep pace with technological advancements, the research and development (R&D) of cutting-edge machinery and equipment become pivotal. This article delves into the latest trends, focusing on key areas such as automation, sustainable practices, and the integration of advanced technologies.
Automation and Robotics
Automation and robotics have transformed industrial operations significantly. The integration of automated systems in manufacturing processes has led to increased efficiency and precision. According to a report by the International Federation of Robotics (IFR) (source), global sales of industrial robots reached 373,000 units in 2021, a clear indicator of the rising adoption of robotics. These robots are designed to perform repetitive tasks with high accuracy, reducing the margin of error and enhancing productivity.
Another notable trend is the development of collaborative robots, or cobots, which work alongside human workers. These robots are equipped with sophisticated sensors and AI capabilities, allowing them to perform complex tasks while ensuring safety and interaction with humans. Companies like Universal Robots have been at the forefront of cobot technology, providing solutions that are easy to integrate into existing workflows (source).
Furthermore, advancements in machine learning and artificial intelligence (AI) have enabled predictive maintenance and real-time monitoring of machinery. This allows for timely interventions before equipment failures occur, significantly reducing downtime and maintenance costs. The integration of AI in industrial machinery is expected to grow, with markets projected to reach $11.2 billion by 2027 (source).
Sustainable Practices in Machinery
Sustainability in industrial machinery is gaining traction as environmental concerns become more pressing. Industries are focusing on reducing their carbon footprint and enhancing energy efficiency. The development of electric and hybrid machinery is a significant step towards sustainable industrial practices. Companies like Caterpillar and Komatsu have introduced electric-powered construction equipment, which drastically reduces emissions compared to traditional diesel-powered machinery (source).
Additionally, the implementation of Industry 4.0 technologies facilitates the optimization of resource usage and waste reduction. Smart factories equipped with Internet of Things (IoT) devices can monitor and control energy consumption, leading to more efficient operations. For example, Siemens’ MindSphere is an industrial IoT-as-a-service solution that helps businesses achieve higher efficiency and sustainability (source).
Recycling and remanufacturing of industrial equipment also contribute to sustainability. By refurbishing old machinery, companies can extend the life cycle of their equipment, reduce waste, and minimize the need for raw materials. The remanufacturing market is estimated to grow at a compound annual growth rate (CAGR) of 6.4% from 2021 to 2028 (source).
Integration of Advanced Technologies
The integration of advanced technologies such as IoT, AI, and augmented reality (AR) is revolutionizing the machinery and equipment sector. IoT enables the connectivity of machines, allowing for seamless communication and data exchange. This connectivity facilitates remote monitoring and control, leading to smarter and more efficient machinery. For instance, General Electric’s Predix platform is an industrial IoT software designed to optimize machinery performance and maintenance (source).
AI and machine learning are also playing crucial roles in advancing machinery capabilities. These technologies enable predictive analytics, which help in anticipating equipment failures and optimizing maintenance schedules. Companies like IBM and Google are leveraging AI to enhance industrial machinery performance and operational efficiency (source).
Augmented reality (AR) is another emerging technology in the industrial sector. AR provides real-time visualization and diagnostics, aiding in training, maintenance, and troubleshooting. An example is PTC’s Vuforia, an AR platform that allows technicians to access real-time data and instructions, improving accuracy and efficiency (source).
Enhanced Safety and Ergonomics
Safety and ergonomics are critical considerations in machinery and equipment research. As industries strive to reduce workplace injuries and enhance worker well-being, the focus on designing safer and more ergonomic machines has intensified. The use of advanced sensors and AI in machinery helps monitor and prevent hazardous conditions. For instance, Honeywell’s safety solutions incorporate real-time monitoring and analytics to mitigate risks and ensure workplace safety (source).
Ergonomics is also a key factor in machinery design, aiming to reduce physical strain on workers. Modern machinery is designed with adjustable components and user-friendly interfaces, making it easier for operators to manage tasks without risking injury. Companies like Bosch Rexroth focus on ergonomics in their machinery designs, providing features that enhance comfort and reduce operator fatigue (source).
Moreover, exoskeletons are emerging as a promising technology to enhance worker ergonomics and safety. These wearable devices support and augment human movements, reducing the physical burden on workers. Companies like Ekso Bionics are leading the way with innovative exoskeleton solutions for industrial applications (source).
Digital Twin Technology
Digital twin technology is transforming the way industries design, operate, and maintain machinery. A digital twin is a virtual replica of a physical asset, system, or process. It allows for real-time simulation and analysis, leading to better decision-making and optimization. According to Gartner, by 2025, over 50% of industrial companies will use digital twins, resulting in a 10% improvement in effectiveness (source).
The application of digital twin technology spans various industries, from manufacturing to healthcare. In manufacturing, digital twins enable the simulation of production processes, identifying potential bottlenecks and optimizing operations. Siemens’ digital twin solutions are widely used in manufacturing to enhance productivity and efficiency (source).
In maintenance and operations, digital twins provide real-time data and predictive analytics, allowing for proactive maintenance and reducing downtime. For instance, GE’s Digital Twin technology is used in aviation to monitor aircraft engines and predict maintenance needs, enhancing reliability and safety (source).
Conclusion:
The landscape of machinery and equipment research is continually evolving, driven by technological advancements and the need for more sustainable and efficient industrial practices. From automation and robotics to digital twin technology, these innovations are reshaping industries and setting new standards. As we move forward, the integration of advanced technologies and a strong focus on sustainability and safety will continue to play a pivotal role in industrial advancements.
Key Takeaways:
- Automation and Robotics: Significant growth in the adoption of industrial robots and collaborative robots (cobots).
- Sustainable Practices: Increasing focus on electric and hybrid machinery, Industry 4.0 technologies, and recycling/remanufacturing.
- Advanced Technologies: Integration of IoT, AI, and AR enhancing machinery efficiency and performance.
- Safety and Ergonomics: Use of advanced sensors, AI, ergonomic designs, and exoskeletons for improved worker safety and well-being.
- Digital Twin Technology: Real-time simulation and analysis transforming industrial design, operation, and maintenance.
FAQs
1. What are the main trends in machinery and equipment research?
- Automation and Robotics: Increasing use of industrial robots and cobots.
- Sustainable Practices: Focus on electric and hybrid machinery, smart factories, and recycling/remanufacturing.
- Advanced Technologies: Integration of IoT, AI, and AR.
- Safety and Ergonomics: Enhanced safety features and ergonomic designs.
- Digital Twin Technology: Real-time simulation and predictive maintenance.
2. How is automation impacting industrial operations?
- Efficiency: Increased precision and reduced error margin.
- Productivity: Higher output with reduced downtime.
- Cost Savings: Lower maintenance costs and operational expenses.
3. What are collaborative robots (cobots)?
- Cobots are robots designed to work alongside human workers, enhancing productivity and ensuring safety.
- Equipped with advanced sensors and AI for interaction with humans.
- Examples: Universal Robots’ cobots.
4. How are industries adopting sustainable practices in machinery?
- Transition to electric and hybrid machinery.
- Implementation of Industry 4.0 technologies for optimized resource usage.
- Recycling and remanufacturing to reduce waste and extend machinery life cycles.
5. What role does AI play in machinery and equipment?
- Predictive maintenance and real-time monitoring.
- Enhanced performance and operational efficiency.
- AI-driven analytics for better decision-making.
6. How is augmented reality (AR) used in industrial machinery?
- Real-time visualization and diagnostics for maintenance and troubleshooting.
- Improved training and accuracy in operations.
- Example: PTC’s Vuforia AR platform.
7. What advancements are being made in machinery safety and ergonomics?
- Use of advanced sensors and AI for real-time safety monitoring.
- Ergonomic designs to reduce physical strain on workers.
- Development of exoskeletons for industrial applications.
8. What is digital twin technology?
- A digital twin is a virtual replica of a physical asset or process.
- Enables real-time simulation and analysis for optimization.
- Used in various industries for design, operation, and maintenance.
9. How does digital twin technology benefit industries?
- Improved decision-making and efficiency through real-time data.
- Proactive maintenance and reduced downtime.
- Enhanced productivity and operational effectiveness.
10. What is the future outlook for machinery and equipment research?
- Continued growth in automation and robotics.
- Increased emphasis on sustainability and energy efficiency.
- Greater integration of advanced technologies like IoT, AI, AR, and digital twins.